A CNC drill incorporates numerous features and geometries that significantly influence its performance, productivity, and longevity when machining specific materials.
Understanding these drill geometries is crucial not only to grasp their impact on applications but also to determine which geometries are ideal when choosing your next drill.
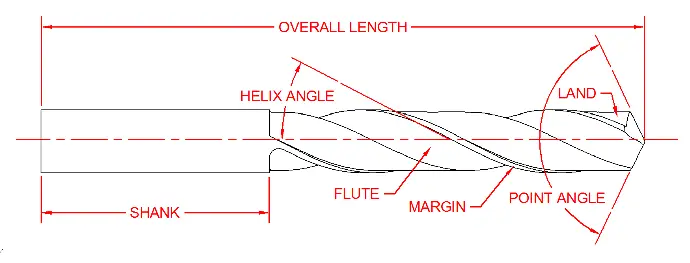
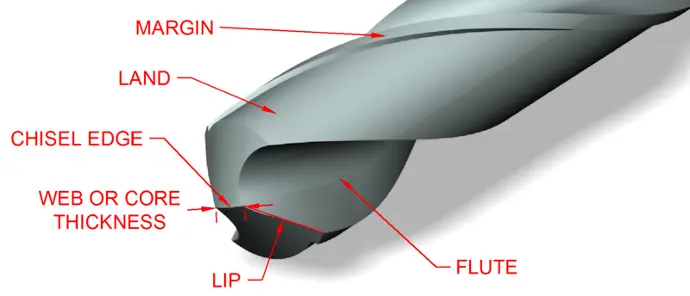
1. Point Angle
This drill geometry pertains to the cutting edge angle, affecting radial forces and material suitability. A smaller angle improves performance in through-hole applications by reducing axial forces, promoting better chip control.
118° & 120° Point Angle:
Often chosen for machining soft and gummy materials.
135° Point Angle:
Ideal for machining aluminum and stainless steels.
140° Point Angle:
Suitable for machining steels.
150° Point Angle:
Used in spot drilling, its selection depends on the final drill angle to prevent drill walking and ensure precision.
Greater angles are frequently employed in spot drilling, yet the ideal spot drill angle hinges on the final drill's angle size. Choosing the correct spot drill is crucial to prevent drill wandering and achieve precise final results.
2. Chisel and Cutting Edges
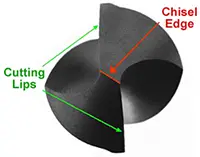
While the chisel edge of a CNC drill does not perform cutting, it plays a critical role in centering the drill by pushing material toward the cutting edges. These cutting edges then initiate chip formation, which moves up through the drill's flutes.
3. Flutes
The flutes are the prominent features of a drill, characterized by deep grooves that facilitate chip evacuation. When envisioning a drill, one typically pictures a spiral flute design. These spiraled grooves complement the drill's point angle, chisel edge, and cutting edges. They function akin to an elevator system, effectively lifting chips out of the hole and ensuring superior chip evacuation. Spiral flutes perform well across various materials, delivering high-quality holes.
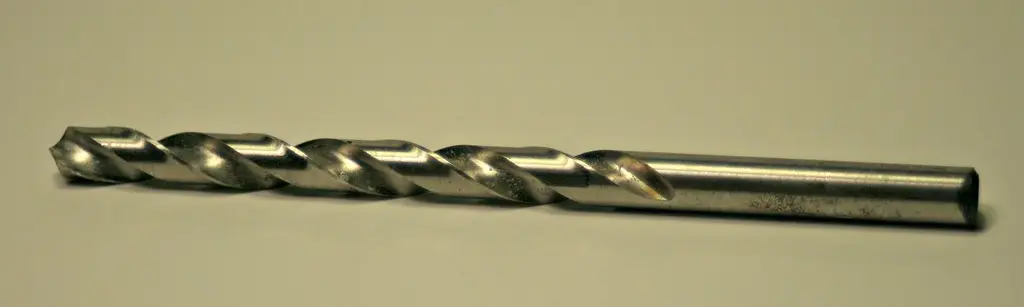
Get Your Free Quote Today
Don't wait any longer on your project!
4. Helix Angle
The helix angle refers to the angle formed between the leading edge of the drill's land and a plane that includes the drill axis. Its primary role is to facilitate the removal of chips from the hole, and the optimal angle depends on the material being machined and the specific application at hand.
Low Helix:
A low helix angle, typically ranging from 12° to 22°, is ideal for materials such as cast iron, brass, and hardened steels. These materials produce shorter chips that flow more freely, aided by coolant to effectively remove them from the hole.
Medium Helix:
Medium helix angles, ranging from 28° to 32°, are widely favored for their balanced performance in chip evacuation and drill strength. They are recommended for general-purpose drilling applications across various materials.
High Helix:
A high helix angle, typically between 34° and 38°, is best suited for long-chipping materials like softer non-ferrous metals such as brass, aluminum, and plastics. Drills with a high helix angle are also advantageous for deep hole drilling, ensuring efficient chip evacuation.
5. Web Thickness (Core)
The web is the central part of the drill body that connects its two flutes. Its thickness directly affects the drill's torsional strength. A drill with a larger web diameter will exhibit greater torsional strength compared to one with a smaller web diameter.
The appropriate web thickness depends on the material being machined. For materials that produce long chips, a drill with a smaller web thickness is needed to ensure sufficient clearance for chip removal. Conversely, when drilling materials like cast iron that produce shorter chips, increasing the drill web thickness enhances its overall strength.
6. Corner Chamfer
A corner chamfer or radius is commonly applied to remove sharp edges where the flutes meet the outside diameter of a drill. This prevents material breakout upon hole exit and reduces the size of entrance and exit burrs. Moreover, this feature is renowned for substantially prolonging tool life.
7. Drill Margin
Margins are the surfaces on the outer diameter of the drill that stabilize the hole by supporting the radial forces exerted by the drill point.
Drill Margin Size:
The width of the margin influences the overall hole quality. Wide margins enhance drill stability, maintain tighter diameter tolerances, and improve hole circularity. Conversely, narrow margins reduce friction and heat, prevent work hardening, minimize built-up edge, and extend tool life.
Number of Drill Margins:
The number of margins on a drill depends on the hole type. Single margin drills are common for uninterrupted holes, while double or triple margins are used for interrupted or intersecting holes. More margins provide better guidance to keep the drill aligned during complex cuts but increase friction, leading to accelerated wear and reduced tool life.
8. Land of a Drill
The land refers to the outer part of the drill body between adjacent flutes. Its width determines the drill's ability to withstand torsional forces before potential failure. A narrower land increases chip space, reducing torsional strength, while a wider land decreases chip space, enhancing torsional strength.
9. Coolant-Through Channels
Coolant-through channels provide numerous benefits to drilling applications and are particularly advantageous for hole depths exceeding 4XD (4 times diameter). These drills enable higher speed and feed rates, enhance lubrication, improve chip control, achieve superior surface finishes, and extend tool life.
10. Shank
Critical
The shank is a crucial yet often overlooked component of a drill, serving as the drive mechanism that mounts into a tool holder. It is vital that the shank meets precise diameter tolerances, taking into account the type of holder used. For instance, a shank with an h6 tolerance is necessary for a shrink fit style tool holder.
Familiarizing yourself with the various geometries of a CNC drill can greatly aid in choosing the appropriate tool for your next project. Understanding how these features function will also enable you to troubleshoot any potential machining challenges that may arise in future CNC drilling tasks.
Accurate Machine Products provides a wide range of manufacturing capabilities and value-added services for all of your prototyping and production needs. Visit our website to learn more or to request a free, no-obligation quote.